Product Name
Metal terminal products are formed by high-speed continuous stamping die or single-engine die stamping of copper alloys. The terminal is the core part of the connector to complete the electrical connection function.
The contact pair is generally composed of a positive contact and a negative contact. The electrical connection is completed through the engagement of the male and female contacts. The positive contact member is a rigid part.
Metal Terminals, Stamping Terminals, Terminal Parts, Metal Terminal Moulds, Precision Hardware Terminals, Metal Stamping Terminals, Terminal Processing, Terminal Processing Manufacturers
Stamping die
1. terminal die design process
1> terminal mold design layout, as much as possible to save the material, under normal circumstances, the material Pitch product or customer has been determined, can not be changed. So consider the width of the material, Can be single material, double row terminals, Dual materials, double plug terminals to increase material utilization.
2> mold design as much as possible in the same step to carry out multiple Process, try to reduce the length of the mold to eliminate the cumulative error produced by the processing accuracy.
3> strict requirements on the bending angle / size, add an adjustment step as much as possible, adjustments only need to be made on the punch press without disassembling the mold.
4>In general, it is to increase the stamping speed and dimensional stability, and to reduce the cost of individual products. The profit of a single product of a terminal product is relatively low, which depends on high output to increase the overall profit.
2. the key technology of terminal stamping die processing
1>High-precision/surface precision grinding
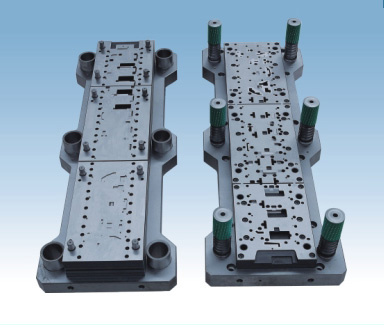
A. Optical projection grinding.
B. High speed reciprocating grinding.
C. mold jig grinding.
D. wipe mirror grinding (Lapping).
2>Wire cut electrical discharge machining (WEDM)
A. Oil type wire cutting discharge machining.
B. Water line cutting discharge machining.
C. Low metamorphic layer wire cutting discharge machining.
3> Mold material and processing technology
A. mold heat treatment technology.
B. PVD, CVD, TD, etc.
C. Superhard mold diamond film coating (Diamond coating).
D. Ultra-fine particle superhard mold.
Technology
Stamping terminal is an important process - punching, it belongs to the separation process, when the workpiece is stressed, it will be elastic deformation, plastic deformation, and end with a break. So, what are some stamping information about blanking terminals? details as follows:
1. The shear section is divided into four characteristic areas, namely Bending fillet, ine zone, torn zone, Burr
2, influence of the gap on the quality of pressed terminal:
(1) Blanking part quality refers to the cutting surface quality, dimensional accuracy, and shape error.
(2). If the gap is too small, it will produce secondary shear. The two ends are ine zone and have burrs on the end surface. although the burr is increased, it is easy to remove, and the workpiece has a small curvature and the cross section is vertical, so the tear is not Very deep, still applicable. However, the gap is too small. The punching force increases. Increased wear reduces die life.
(3) In the material band, punch out the terminal head hole;
(4) The copper wire is riveted and welded to form a terminal at the end of the terminal head;
(5), a plating treatment is performed to the terminal;
(6) Bend the terminal and remove the material band to make a product.
The product structure process has been improved, the difficulty of processing has been greatly reduced, the processing time has been greatly shortened, and the total production energy consumption has been significantly reduced.
3, mold maintenance
Kang Ding introduced imported metal mold processing equipment, regular hardware mold maintenance, the establishment of the corresponding spare parts risk inventory, to ensure the stability of precision stamping terminal product delivery.
application
The terminal block is a kind of connector and it is an important component in the electrical industry. It plays an irreplaceable and non-negligible role. Because the engineers and technicians first check the interface during the inspection, that is, the terminal, the terminal block The design is particularly important.
Electrical appliances, information products, automobiles, motorcycles, aviation and navigation areas, nuclear power, telephones, mobile phones, PC computers, medical supplies, lighting, telephones, plush toys, and electric toys. Anti-theft products, radios, digital cameras, lithium batteries, electronic dictionaries, a la carte machines, and various small electronic products.
material
Common materials: phosphor bronze, copper, bronze, brass, beryllium copper, stainless steel and other metals
technical standard
(1) Development and application of multi-cavity terminals: For example, DDR240P terminal common company only develops 2x4 as 8, and currently our company developed 16x for 2x8, and the use of plug-in test mold structure material width reduced from 26.5mm to 21.0mm can save 17.5% of the material, the speed increase from the general 500 to 650 can fully save customers the material and time cost.
(2) MINI-PCI design pitches 0.60mm.. This can save a lot of materials, greatly reducing the volume of the final product. This can make the product smaller and smaller, the accuracy is getting higher and higher.
(3) High-speed stamping: At present, the stamping speed of our company can reach more than 1200 times per minute, that is, a 16-cavity mold can produce 15KK terminals a day.
(4) Terminal tolerance standard: Generally, the tolerance of the terminal is within +/-0.10MM, and some require tight tolerance control of +/-0.04, but our company can achieve +/-0.01MM. This tolerance is The mold requirement is very high.
(5) Stamping ultra-thin material: The thickness of the material processed by a general company is 0.15mm to 0.50mm, but our company can process materials with a minimum thickness of 0.08mm. The processing accuracy of this kind of thin material mold is one grade higher than usual.
(6) Stamping ultra-thick, hard material: The general material is thicker and harder, and it is easy to wear the punch and knife edge. Therefore, we use better mold steel and can process materials with a material thickness of 0.8 or more.
(7) Press section finish: For the connector, the better the finish of the contact surface, the smaller the impedance, the smaller the surface wear, the more durable the product, and the more stable the transmission signal. The bright surface of the terminal surface we produce reaches more than 95%.
(8) Punching terminal flash control standard: The general terminal burr is controlled within 0.04mm, but the terminal produced by our company can be controlled within 0.01. In this way, the plastic and the terminal are not scratched during the assembly, and the gold-plated surface is not scratched during the contact, which is conducive to the stability of the electrical conduction.
Detector
Terminals have been widely used in various fields, and have played a connecting role in the transmission of electrical signals and electrical conduction, thereby reducing the workload and the cost of production, bringing convenience to production and use, and avoiding many problems.
In order to simplify the product structure and save manufacturing costs. Therefore, for the benefits of terminal detection combined with market analysis, it is recommended that instruments suitable for terminal detection can be tested with professional inspection equipment. Commonly used terminal detection devices include: tool microscopes and optical imagers.